Last Updated on 11 7 月, 2025 by
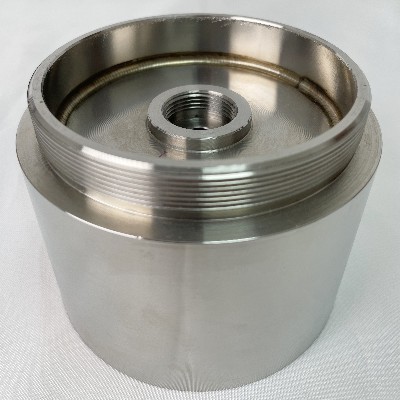
In heavy-duty sectors like construction machinery, hydraulic systems, and food/pharmaceutical equipment, stainless steel machined parts serve as the “skeletal joints” of machinery, where precision and strength dictate overall lifespan. Centered on 5-axis mill-turn technology and micron-level dimensional chain control, we engineer precision stainless steel components that conquer thousand-ton pressures and millimeter assembly tolerances—ensuring mechanical hearts beat eternally under extreme conditions.
I. Machining Challenges & Breakthrough Solutions for Heavy-Duty Mechanics
Critical Failure | Traditional Flaws | Our Technological Edge |
---|---|---|
Stress Fracture | Micro-cracks from vibration | Vibration-dampening toolholders + residual stress relief |
Assembly Interference | Cumulative error >0.2mm | Closed-loop dimensional control ±0.01mm |
Corrosion Fatigue | Passivation layer damage | Integrated machining-passivation process |
Wear Failure | Surface hardness <HRC30 | Cryogenic hardening (HRC45↑) |
II. Six Core Processes: Redefining Stainless Steel Machining Limits
-
Material Genome Selection
Application Recommended Material Performance Edge Acidic Environments 2205 Duplex Steel PREN≥35 pitting resistance Heavy-Duty Bearings 17-4PH Precipitation Hardening Aged hardness HRC44 Food-Grade Contact 316L VIM-VAR Sulfur content <0.001% Wear-Resistant Tracks Nitronic 60 High-Nitrogen Steel 3x wear resistance vs. 304 -
5-Axis Mill-Turn Matrix
-
Capability Topology: [Turning-Milling] — [B-Axis Swivel] — [In-Process Metrology] — [Adaptive Compensation]
-
Max Workpiece:
✓ Turning: Φ1200mm × 3000mm
✓ Milling: 2000mm × 800mm × 600mm -
Precision Pinnacle:
▶ Positional tolerance ±0.005mm
▶ Cylindricity 0.003mm/100mm
▶ Surface roughness Ra 0.4μm (as-machined)
-
-
Micron-Level Process Chain
-
Closed-Loop Flow: [Roughing (0.5mm stock)] → [Vibration stress relief] → [Semi-finishing] → [Cryogenic stabilization] → [Micron-finishing]
-
Deformation Control: Large frame flatness ≤0.02mm/m²
-
Deep-Hole Drilling: Φ3mm×200mm hole straightness 0.02/100mm
-
-
Specialized Surface Enhancement
Technology Application Performance Gain Cryogenic Treatment Bearing seats/gears Wear resistance ↑300% Micro-Arc Oxidation (MAO) Hydraulic valve blocks Corrosion resistance = Hastelloy Laser Cladding Shaft journal repair Bond strength >600MPa -
In-Process Quality Fortress
-
Machine Probe System:
✓ Real-time tool wear compensation
✓ 100% key dimension inspection (replaces CMM) -
Smart Tool Monitoring:
▶ Acoustic emission for breakage detection
▶ Cutting force overload alert
-
-
Cleanliness Control
-
Medical-Grade Cleaning:
✓ Pure water ultrasonic wash (residual particles <5/m²)
✓ Vacuum drying (dew point -70°C) -
Cleanroom Packaging: Class 100 nitrogen-purged sealing
-
III. Iconic Components for Kiloton Applications
Component | Critical Parameter | Breakthrough Process |
---|---|---|
2000T Hydraulic Column | Straightness 0.05mm/8m | Ultra-long shaft mill-turning |
TBM Main Bearing Housing | Flatness 0.02mm/Φ2000mm | Thermostatic machining + multi-point fixturing |
Food Filling Valve Block | 316L mirror finish Ra 0.2μm | Diamond tool precision turning |
Wafer Handler Joint | Repeat positioning ±1μm | Micron-level hole matching |
IV. Technological Moats: Why Global Heavyweights Choose Us
-
Digital Twin Factory:
✓ AI-optimized cutting parameters (40% efficiency gain)
✓ Thermal deformation compensation simulation (error <3μm) -
Certification Pyramid:
▶ ISO 13485 medical components
▶ ASME B31.3 pressure piping
▶ DNV-GL marine certification -
Extreme Manufacturing Ecosystem:
✓ 40+ 5-axis/mill-turn centers
✓ 2000-ton cryogenic treatment system
✓ Class 100 clean packaging
V. Military-Grade Delivery Protocol
-
Drawing Analysis: DFM report within 72hrs (cost optimization)
-
Process Simulation: Cutting simulation video + deformation data
-
Transparent Production: Real-time key process video sharing
-
Zero-Defect Delivery:
o Full-dimension inspection report (metrology traceability)
o Material composition/mechanical certs
o Surface roughness/residual stress maps -
Lifetime Support:
▶ 48hr emergency spare response
▶ Wear part remanufacturing
Steel-Cast Frameworks, Micron-Controlled Precision.
When a 0.01mm bearing clearance decides the fate of a 10,000-ton press,
When a Ra 0.4μm valve surface impacts pharmaceutical purity,
We redefine heavy machinery’s performance frontier—with micron accuracy, carrier-grade strength, and wafer-level cleanliness.