Last Updated on 4 7 月, 2025 by
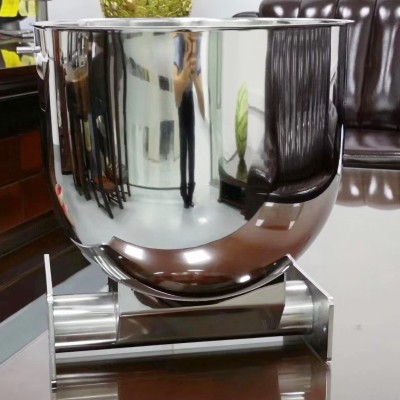
In cutting-edge fields like new energy battery casings, precision sensor housings, and minimally invasive medical devices, flawless welding of complex stainless steel structures is critical to product performance. Leveraging high-power fiber lasers and intelligent process chains, we conquer three welding challenges—stamping springback stress, uneven wall thickness in drawn parts, and high reflectivity of CNC-machined materials—achieving micron-level thermal distortion control and aerospace-grade sealing integrity.
I. Welding Challenges & Laser Breakthroughs for Three Substrates
Component Type | Critical Challenge | Laser Welding Solution |
---|---|---|
Stamped Parts | Springback-induced incomplete fusion | Adaptive fixturing + laser wire filling |
Drawn Parts | >0.2mm wall variation → burn-through | Power-gradient algorithm + penetration monitoring |
CNC Parts | Reflectivity-induced energy fluctuation | Blue laser (450nm wavelength) |
II. Laser Welding Process Matrix: Precision-Tailored Applications
-
Ultra-Thin Welding (0.1–0.5mm)
-
Applications: Sensor hermetic cavities ■ RF shields ■ Implantable electrodes
-
HAZ <50μm, distortion ≤0.01mm
-
Hermeticity: Helium leak rate <5×10⁻¹² mbar·L/s
-
-
Deep-Penetration Welding (1–8mm)
Innovation Technical Edge Typical Use Oscillating Laser ↑40% bead width, ↓90% porosity Battery module endplates Dual-Beam Synergy Spatter suppression, ±3% depth stability Hydraulic valve sealing Hybrid Penetration Monitoring Plasma spectroscopy + IR thermography Nuclear fuel cladding tubes -
Dissimilar Material Joining
-
Example: 316L stamped case + Hastelloy CNC nozzle
-
Process chain: Laser cleaning → Ni-based filler → Power ramp control
-
Shear strength >350MPa (85% base metal)
-
Passes ISO 17643 corrosion cross-test
-
III. Four-Dimensional Quality Fortress: From Nano-Defects to Macro-Deformation
-
Smart Preprocessing
-
3D vision positioning: ±0.02mm gap detection
-
Laser cleaning: Removes 3nm oil film (contact angle <5°)
-
Stress relief: Vibration aging ↓80% residual stress
-
-
Real-Time Monitoring
-
Closed Loop: [Molten pool imaging] → [Plasma analysis] → [AI parameter adjustment] → [IR thermography]
-
Penetration fluctuation control ±0.05mm
-
Spatter particles <5/meter weld
-
-
Zero-Distortion Tooling Revolution
-
Water-cooled contour fixtures: 0.1mm/m thermal compensation
-
Magnetic adaptive fixturing: Conforms to curved surfaces
-
-
Holographic NDT
Technique Defect Resolution Application Industrial CT Φ0.05mm pores Complex internal structures Lock-in IR Thermography 0.1mm lack of fusion Multi-layer welding EBSD Crystallography HAZ grain growth monitoring Nuclear critical welds
IV. Legendary Laser Welds for Advanced Manufacturing
Industry | Component | Breakthrough Metric |
---|---|---|
New Energy | 4680 Battery Can | 8m/min speed, >3MPa burst pressure |
Medical Tech | Endoscope Articulation | Ø0.8mm hinge weld fracture-free |
Semiconductor | Etcher Gas Manifold | >5-year HF corrosion resistance |
Aerospace | Turbofuel Nozzle | Zero leakage after 2000 thermal cycles |
V. Technological Moats: Mastery of Laser Welding Extremes
-
Multi-Wavelength Laser Matrix:
✓ IR fiber laser (1064nm): Deep penetration
✓ Blue laser (450nm): Conquers reflective metals
✓ Green laser (515nm): Ultra-thin precision -
Digital Twin Welding Lab:
▶ Molten pool fluid dynamics simulation (>95% accuracy)
▶ AI thermal distortion compensation -
Certification Pyramid:
✓ ISO 13919-1 laser weld standard
✓ NADCAP WLD special materials
✓ IATF 16949 automotive
VI. Accelerated Smart Manufacturing
-
Weldability First: Free material weldability report
-
Process Simulation: Thermal distortion video + parameter package
-
Transparent Production: Real-time welding video access
-
Zero-Defect Delivery:
o Weld metallography report
o 3D industrial CT scan
o Fatigue life certification (IIW standard) -
Lifetime Guarantee: 10-year leak warranty for critical welds
Light as Blade, Intelligence as Core.
When 0.1mm distortion cripples precision instruments,
When nanoscale pores collapse vacuum systems,
We forge eternal bonds for advanced manufacturing—
With femtosecond-level control, atomic-scale cleanliness, and steel-clad reliability.