Last Updated on 28 6 月, 2025 by
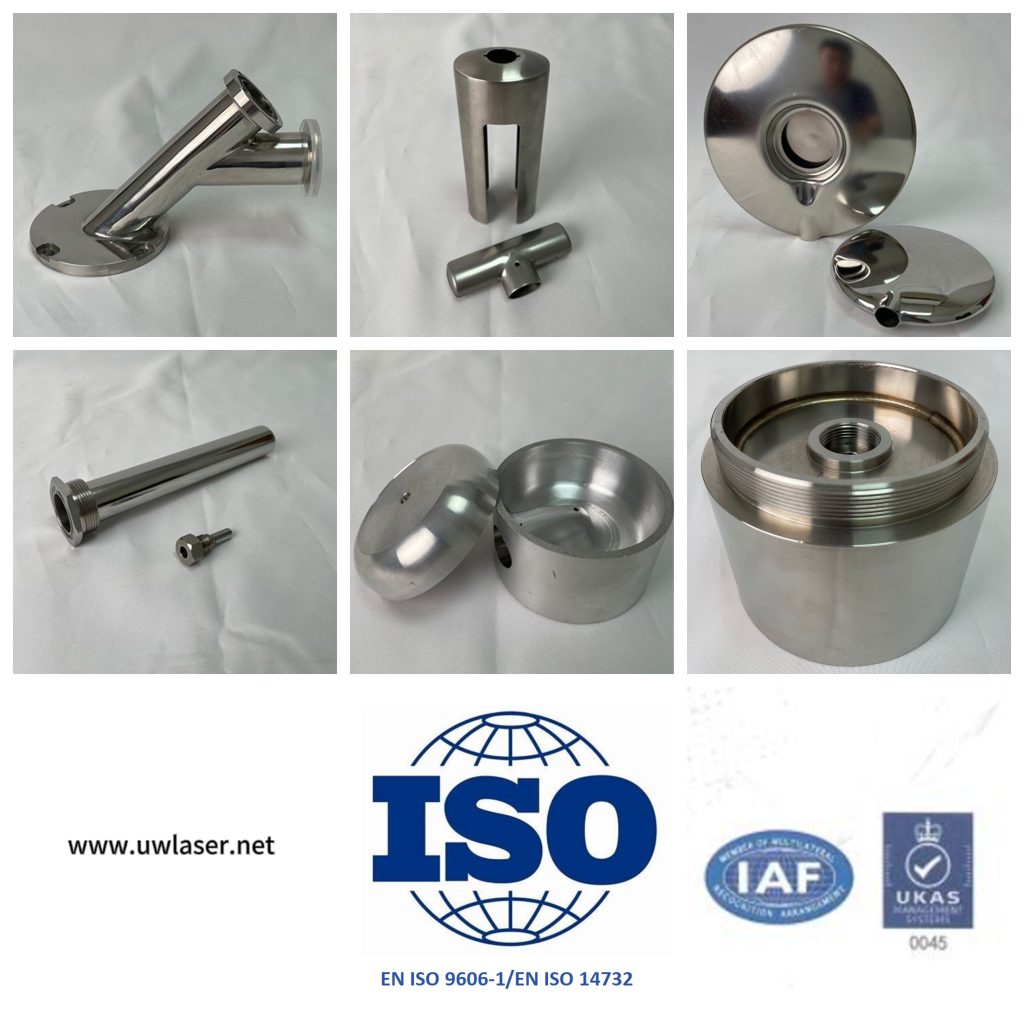
Precision Fabrication for Global Industries
1. Core Manufacturing Processes
Our stainless steel welding integrates advanced techniques to ensure corrosion resistance, structural integrity, and aesthetic excellence:
🔧 Key Welding Methods:
-
TIG (GTAW) Welding
-
For aerospace, medical & food-grade applications (e.g., pipes, vessels).
-
Argon shielding gas | Precision heat control | Autogenous welds possible.
-
-
MIG (GMAW) Welding
-
High-speed fabrication of structural components (racks, frames).
-
Pulsed MIG for thin sheets (<1mm) | Low spatter.
-
-
Laser Hybrid Welding
-
Automotive/exhaust systems | Seamless high-strength joints | ≤0.1mm precision.
-
-
Plasma Arc Welding (PAW)
-
Critical thickness control (e.g., pressure vessels).
-
⚙️ Ancillary Processes:
-
Post-Weld Treatment
-
Pickling & Passivation: Restore corrosion resistance using HNO₃/HF solutions.
-
Electrochemical Polishing: Mirror finishes for sanitary applications (ISO 9001/ASME BPE compliant).
-
-
Distortion Control
-
Jig/fixture optimization | Step-back welding sequence | Thermal stress simulation.
-
2. Critical Technical Challenges & Solutions
Challenge | Root Cause | Our Solution |
---|---|---|
Heat-Affected Zone (HAZ) Corrosion | Chromium carbide precipitation | ▶ Low-carbon grades (316L) ▶ Laser overlay welding ▶ Interpass temp ≤150°C |
Warping/Deformation | Uneven thermal expansion | ▶ Modular clamping systems ▶ Pre-set counter deformation ▶ Robotic pulse welding |
Porosity & Cracking | Contamination (O₂, S, oils) | ▶ Triple-stage degreasing ▶ Ultra-dry shielding gas (dew point -60°C) ▶ Ferrite control (FN 4-12) |
Weld Discoloration | Oxide layer formation | ▶ Back-purging (O₂ < 0.1%) ▶ Post-weld electropolishing |
Thin-Gauge Burn-Through | Excessive heat input | ▶ Pulsed arc technology ▶ 0.3-1.0mm auto-gap compensation |
3. Quality Assurance System
-
Certifications: ISO 3834-2, EN 1090-EXC3, PED 2014/68/EU
-
Testing Protocols:
-
NDE: 100% X-ray (EN ISO 17636) | Dye penetrant (ASTM E165)
-
Mechanical: Tensile/bend tests (ASTM A370) | Salt spray testing >1,000hrs (ASTM B117)
-
Metallurgical: HAZ microanalysis | Ferrite scope verification
-
4. Industry Applications
✅ Food & Pharma: CIP/SIP-ready vessels | EHEDG-compliant seams
✅ Energy: Offshore platform fittings | Desalination plant tubing
✅ Architecture: Seamless handrails | Structural façades (AWS D1.6 compliant)
✅ Transport: Lightweight cargo systems | Exhaust SCR assemblies
5. Competitive Advantages
-
Material Expertise: Dual-certified 304/316, super duplex (UNS S32750), nickel alloys
-
Smart Manufacturing:
-
AI-powered weld monitoring (real-time defect detection)
-
Automated seam tracking (±0.05mm repeatability)
-
-
Supply Chain Flexibility:
-
Cut-to-size laser profiling | Just-in-time delivery | Global logistics support
-
Contact us today for corrosion-resistant solutions that meet ASME, DIN, and JIS standards!
[Your Company] – Where Precision Welding Meets Global Reliability.