Last Updated on 11 7 月, 2025 by
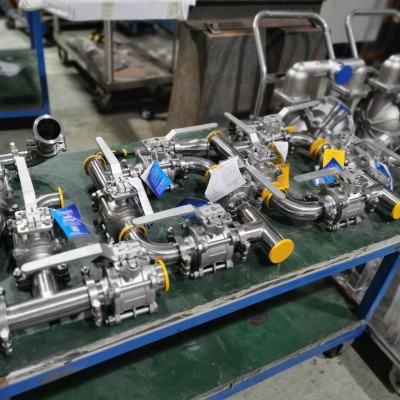
In high-end manufacturing sectors like lithium battery cathode materials, food additives, and pharmaceutical powders, 0.1% batching accuracy and residue-free conveyance are critical lifelines for quality. Integrating aerospace-grade stainless steel technology with intelligent flow control, we engineer modular loss-in-weight feeding systems that conquer nanoscale powders. With microgram-level weighing stability, zero-bridging fluidization, and sterile-grade cleanliness, we redefine the precision limits of powder processing.
I. The Critical Battle of Powder Batching
Industry Challenge | Traditional Solution Flaws | Our Disruptive Resolution |
---|---|---|
Accuracy Drift | Screw feeder error >1% | Loss-in-weight dynamic compensation ±0.1% FS |
Powder Bridging | Vibrators damage crystal structure | Micro-frequency air hammer + fluidized bed design |
Cross-Contamination | Dead-leg residue >50g/batch | Fully welded, mirror-polished surface Ra≤0.2μm |
Corrosion Failure | Carbon steel rust contaminates material | 316L ultra-low carbon stainless steel matrix |
II. Modular Stainless Steel Technology Fortress
-
Core Loss-in-Weight Module
-
Structural Topology: [Load Cell] — [Anti-Vibration Suspension] — [AI Temperature Compensation]
-
Microgram Stability:
-
✓ Triple-beam load cell (C3 accuracy, resolution 0.02g)
-
✓ Air spring vibration isolation (>90% attenuation @ 5Hz)
-
✓ Real-time thermal drift compensation (±0.5g/10°C)
-
-
Sanitary Design:
-
▶ IP69K protection rating
-
▶ Tool-free quick-release dust cover (<30s removal)
-
-
-
Zero-Residue Fluidized Conveying Module
Component Innovation Performance Metric Fluidized Bed Microporous sintered plate (Φ0.3μm) Gas permeability uniformity >98% Anti-Bridging System Piezoceramic high-frequency vibrators (50kHz) Bridging energy consumption <10W Pneumatic Conveying Pipe Large-radius bend (R/D=5) Residue <0.01g/m -
Ultra-Clean Structural Genome
-
Material Matrix:
-
✓ Main structure: 316L ELV (Extra Low Vacuum degassed steel)
-
✓ Contact surfaces: S31803 duplex steel (↑300% wear life)
-
✓ Seals: PTFE-encapsulated fluororubber (powder abrasion resistant)
-
-
Surface Revolution:
-
▶ Electro-polishing (EP) Ra≤0.2μm (FDA 21 CFR 177.1520 compliant)
-
▶ Nano-silicon coating (surface energy <20mN/m, anti-adhesion)
-
-
-
Intelligent Control Hub
-
Control Logic Chain: [Real-time weight loss rate monitoring] → [PID adaptive compensation] → [Gas-solid coupling model] → [Predictive anti-jamming]
-
Precision Assurance:
-
✓ 100Hz sampling rate, filter algorithms eliminate mechanical vibration noise
-
✓ Batch-to-batch repeatability RSD <0.15%
-
-
IoT Empowerment:
-
▶ OTA remote recipe updates
-
▶ >99% accuracy in material bridging warnings
-
-
III. Modular Architecture for Demanding Applications
Application Scenario | Core Challenge | Our Solution |
---|---|---|
CNT Conductive Additives | Electrostatic adhesion + poor flow | Anti-static surface coating + dry fluidizing gas |
Vitamin Premixes | Thermal sensitivity + hygroscopic | N₂ blanketed fluidization + dew point control <-40°C |
Lithium Oxide Cathode Material | High corrosivity + particle sensitivity | Hastelloy C276 fluidized bed + online laser particle sizing |
Sterile APIs | Cross-contamination risk | CIP/SIP in-place sterilization (SIP 121°C/30min) |
IV. Technological Moat: Defining Powder Industry 4.0
-
Multiphysics Simulation:
-
✓ DEM powder flow simulation (EDEM software)
-
✓ Structural stress-vibration modal analysis (error <5%)
-
-
Certification Pyramid:
-
▶ cGMP (Current Good Manufacturing Practice)
-
▶ ATEX explosion-proof certification (Zone 21 dust environment)
-
▶ OIML R61 weighing certification
-
-
Rapid Response Ecosystem:
-
✓ Modular assembly (field installation <4 hours)
-
✓ Digital twin O&M platform (>72h fault prediction)
-
V. Accelerated Delivery Process
-
Process Diagnosis: Provide material properties (angle of repose / bulk density / PSD)
-
Modular Design: Real-time solution generation via 3D configurator
-
Prototype Validation: 72-hour live material testing
-
Smart Delivery:
-
Material Traceability Report (EN 10204 3.1)
-
Calibration Certificate (NIST traceable)
-
-
Intelligent O&M:
-
▶ AR-assisted remote guidance
-
▶ Smart consumables alert & delivery
-
Cosmos in Particles, Precision in Milligrams.
When a 0.1g batching error ruins tons of battery slurry, when a single speck contaminates an entire pharmaceutical line, we establish the absolute benchmark for powder industry—with microgram sensing precision, nanoscale surfaces, and intelligent flow control algorithms.