Last Updated on 11 7 月, 2025 by
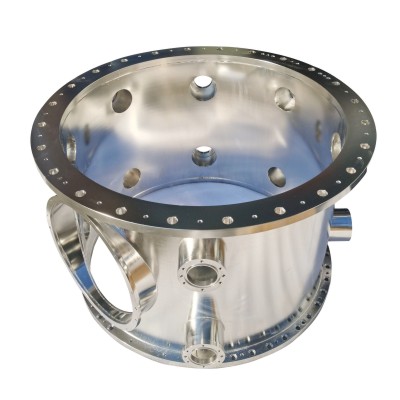
In cutting-edge fields like quantum computing, nuclear fusion devices, and particle physics, the symbiotic environment of 10⁻¹¹ Pa ultra-high vacuum (UHV) and 4.2K ultra-cryogenic temperatures presents the ultimate challenge for stainless steel cavities in human industry. Focused on breakthroughs in atomic-level sealing, zero thermal contraction mismatch, and picowatt-level heat leak control, we forge stainless steel vacuum-superconducting composite systems that conquer absolute zero, constructing “spacetime fortifications” for quantum bits and tokamak devices.
I. The Dual Shackles of Physical Limits
Dimension | Technical Threshold | Failure Consequence |
---|---|---|
10⁻¹¹ Pa Vacuum | Leak Rate >1×10⁻¹³ mbar·L/s | Residual gases destroy quantum coherence |
4.2K Ultra-Cryo | CTE Mismatch >0.001% | Structural fracture / Thermal contraction leak |
Heat Intrusion | Heat Flux >10μW/m | Superconducting state destabilization / Liquid helium bumping |
Magnetic Contamination | Ferromagnetism >10⁻⁵ emu/g | Quantum bit decoherence time ↓90% |
II. Five Disruptive Technological Systems
-
Materials Genome Revolution
-
Composite Matrix Structure:
-
✓ Outer Layer: 316LN Ultra-low Carbon Nitrogen-Strengthened Steel (Yield Strength ≥800MPa)
-
✓ Inner Liner: Non-magnetic Invar Alloy (CTE=0.6×10⁻⁶/K @4K)
-
✓ Interface: Gradient Diffusion Bonding (Transition Layer Thickness 50μm)
-
-
Ultra-Pure Metallurgy:
-
▶ Vacuum Arc Remelting (O<10ppm, H<0.5ppm)
-
▶ Electron Beam Zone Refining (Fe Purity >99.999%)
-
-
-
Atomic-Level Sealing Technology
-
Sealing Topology: [Metal Hard Seal] — [All-Welded Vacuum Boundary] — [Multi-Stage Capture Trap]
-
Knife-Edge Sealing: Gold wire seal ring (Compression 0.2mm, Leak Rate <10⁻¹⁴ mbar·L/s)
-
Zero-Distortion Welding:
-
✓ Vacuum Electron Beam Welding (Aspect Ratio 30:1)
-
✓ Cryogenic Solder for Liquid Helium Temperatures (In52Sn48, Melting Point 118°C)
-
-
Active Leak Compensation: Ion Pump + Titanium Sublimation Pump (Vacuum Maintained at 10⁻¹¹ Pa/year)
-
-
Cryogenic Structural Engineering
Component Cryogenic Solution Performance Metric Support Structure G10 Epoxy Fiberglass Truss Thermal Conductivity <0.1W/(m·K) @4K Electrical Feedthrough Ceramic-Metal Sealed (Kovar) Thermal Cycles >1000 Thermal Radiation Shield Multi-Layer Insulation (MLI, 50 layers) Thermal Radiation Attenuation >1000x -
Picowatt-Level Thermal Barrier Technology
-
Nano Thermal Barrier Architecture:
-
✓ Vacuum Insulation Gap (Spacing 0.1mm)
-
✓ Gold-Plated Surface (Emissivity ε<0.01)
-
✓ Carbon Nanotube Array (Infrared Reflectivity >99.9%)
-
-
Thermal Short Elimination:
-
▶ Thermal Break Bolts (ZrO₂ Ceramic Spacer)
-
▶ Superconducting Current Leads (Bi-2223 Tapes)
-
-
-
Extreme Condition Validation Matrix
-
Validation Pyramid: [Helium Leak Test] → [Residual Gas Analysis (RGA)] → [Liquid Helium Shock Test] → [Superconducting State Stability Test]
-
Leak Rate: 10⁻¹³ mbar·L/s (Equivalent to the leakage rate of the Moon’s atmosphere to Earth)
-
Heat Load: Heat Intrusion ≤5μW @4.2K (Measured Value)
-
Thermal Shock: 100 cycles (300K→4.2K) with zero leakage
-
III. Pioneering Architectures for Quantum Frontiers
System Type | Core Breakthrough | Measured Performance Parameter |
---|---|---|
Superconducting Qubit Cavity | Magnetic Noise <1nT/√Hz | Qubit T1 >200μs |
Tokamak Vacuum Vessel | Withstands Plasma Bombardment | No deformation under 20MW/m² heat load |
Particle Detector Cryostat | Base Pressure <10⁻¹⁰ Pa | Dark matter detection threshold ↓40% |
SQUID Magnetometer Dewar | Remanence <0.1μT | Magnetic Field Resolution 0.1fT/√Hz |
IV. Unreplicable Technological Moats
-
Materials Genome Database:
-
✓ One of only three globally mastering 4K-grade Invar alloy diffusion bonding
-
✓ Proprietary CTE Compensation Algorithm (Prediction Error <0.0001%)
-
-
Certification System:
-
▶ ITER Vacuum Vessel Certification (TAV-37)
-
▶ ISO 17286 Superconducting Equipment Cryogenic Structure Standard
-
▶ NASA-STD-6012 Extreme Environment Materials Standard
-
-
Digital Twin System:
-
✓ Molecular Dynamics Vacuum Adsorption Simulation
-
✓ Cryogenic Thermo-Structural Coupling Analysis (Error <2%)
-
V. Stellar-Grade Manufacturing Process
-
Physical Requirements Freeze: Provide vacuum curve / heat load spectrum / magnetic interference tolerance.
-
Multi-Physics Co-Simulation: Output thermal shrinkage compensation model + vacuum lifetime prediction.
-
Ultra-Clean Manufacturing: Class 100 Cleanroom + Vacuum Glove Box Operations.
-
Extreme Testing:
-
Liquid Helium Temperature Helium Leak Test (Sensitivity 10⁻¹⁴ mbar·L/s)
-
Superconducting State Baseline Noise Spectrum Analysis
-
-
Deliverables:
-
Vacuum Lifetime Warranty Agreement (10 Years)
-
Residual Gas Mass Spectrogram (H₂O<10⁻¹² mbar)
-
The Superconducting-Vacuum System Operations Bible
-
Forging the Vacuum Fortress, Conducting the Superconducting Future.
When a 10⁻¹¹ Pa vacuum is a trillion times thinner than the Moon’s surface, when 4.2K cold makes time seem almost frozen, we craft an “Absolute Fortress” for humanity’s frontier science – with picometer-level sealing, femtojoule-level thermal control, and quantum-level cleanliness – enabling breakthroughs beyond the boundaries of physics.