Last Updated on 4 7 月, 2025 by
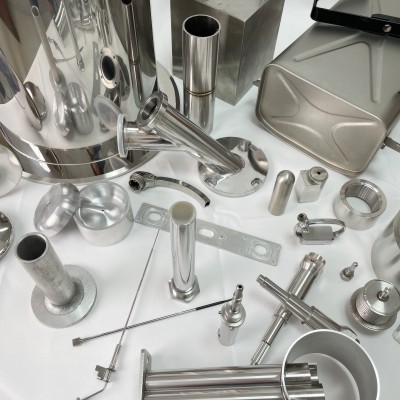
In mission-critical fields like nuclear primary pipelines, aero-engine fuel chambers, and implantable medical devices, weld quality is the lifeline. With laser-TIG hybrid welding technology as our core blade, combining deep penetration and flawless formation, we forge zero-defect stainless steel welds—conquering challenges from 0.1mm ultra-thin foils to 300mm heavy vessels.
I. Hybrid Welding: A 1+1>2 Technological Revolution
Process Comparison | Traditional TIG | Traditional Laser | Laser-TIG Hybrid |
---|---|---|---|
Penetration Depth | <10mm (multi-pass) | 25mm single-pass | 40mm single-pass |
Heat Input | Large HAZ (>3mm) | Low heat input (HAZ<0.5mm) | HAZ=1.2mm |
Formation Quality | Reinforcement >1.5mm (requires grinding) | High undercut risk | 0.3mm reinforcement (ready-to-use) |
Speed Efficiency | 0.3 m/min | 2 m/min | 1.5 m/min |
II. Hybrid Process Matrix: Precision-Tailored for Eight Scenarios
-
Ultra-Thin Precision Welding (0.1–1mm)
-
Applications: Pacemaker hermetic seals ■ Fuel cell bipolar plates ■ MEMS sensor cavities
-
Focus diameter 0.05mm, thermal distortion <10μm
-
Helium leak rate <1×10⁻¹² mbar·L/s
-
-
Dissimilar Material Joining
Material Combination Core Technology Joint Strength 316L-Titanium Laser cleaning + interlayer brazing >85% base metal 304-Copper Blue laser + synchronized wire feed Conductivity loss <3% Duplex Steel-Hastelloy Precise heat input zoning Pitting resistance = base metal -
Heavy-Duty Deep Penetration (>50mm)
-
Applications: Nuclear pressure vessels ■ Liquid hydrogen tanks ■ 10,000-ton hydraulic cylinders
-
40% reduction in groove fill volume
-
100% UT Class I acceptance rate
-
-
3D Curved Surface Welding
-
Robotic synergy system:
✓ 15° leading laser tilt stabilizes molten pool flow
✓ Real-time seam tracking (±0.03mm precision) -
Case studies:
▶ Aero-engine scroll casings (curved assembly)
▶ Marine propeller hubs (martensitic stainless steel)
-
III. Four-Dimensional Quality Fortress
-
Material-Science Grade Preprocessing
-
Laser cleaning: Removes 3nm oxide layer (Sa≤0.5μm)
-
Smart groove monitoring: 3D vision detects ±0.05mm gap tolerance
-
-
AI-Powered Process Control
-
Adaptive Logic: [Molten pool monitoring] → [Plasma spectral analysis] → [Dynamic laser power/arc voltage adjustment]
-
Bead width variation <±0.1mm
-
Porosity <0.1 pore/meter
-
-
Holographic NDT
Technique Capability Ultimate Precision Phased Array UT (PAUT) Defect location + sizing Φ0.3mm holes Industrial CT 3D defect reconstruction 5μm resolution Residual stress mapping Full-field stress cloud Error <10MPa -
Post-Processing Enhancement
-
Laser Shock Peening (LSP): 8x fatigue life improvement
-
Electro-polishing (EP): Weld Ra reduced to 0.2μm
-
IV. Legendary Welds for Extreme Service
Field | Component | Breakthrough Metric |
---|---|---|
Implantable Med | Joint prosthesis base | Passes ISO 5832-1 cytotoxicity |
Superconducting | LHe dewar weld | 4K leak rate <10⁻¹³ mbar·L/s |
Semiconductor | Etch chamber | >10-year Cl₂ corrosion resistance |
Deep-Sea | 10,000m pressure hull | Zero deformation at 1100MPa hydrostatic pressure |
V. Unmatched Technological Moats
-
Digital Twin Welding Lab:
✓ Multiphysics simulation (molten pool hydrodynamics + thermal stress)
✓ 90% faster parameter optimization -
Certification Pyramid:
▶ ISO 15614-11 hybrid welding certification
▶ ASME BPVC Section IX
▶ NADCAP Weldment special process -
Smart Production Matrix:
▶ 20 fiber laser-arc hybrid workstations
▶ 100TB welding big-data repository
VI. Military-Grade Delivery Protocol
-
Weld First: Free Welding Procedure Qualification (WPQ) samples
-
Digital Rehearsal: Output weld distortion simulation report
-
Process Transparency: 24/7 video monitoring at critical stations
-
Traceable Delivery:
o Weld metal chemical composition report
o All-position RT/UT inspection records
o Residual stress distribution cloud -
Lifetime Warranty: Fatigue life calculation model provided
Where Light and Arc Converge, Weld Limits Redefined;
Strength and Grace Combined, Metal Legends Rewritten.
While traditional welding struggles to balance penetration and low distortion, we forge century-defining perfect seams—harnessing the precision of lasers and the versatility of arc.